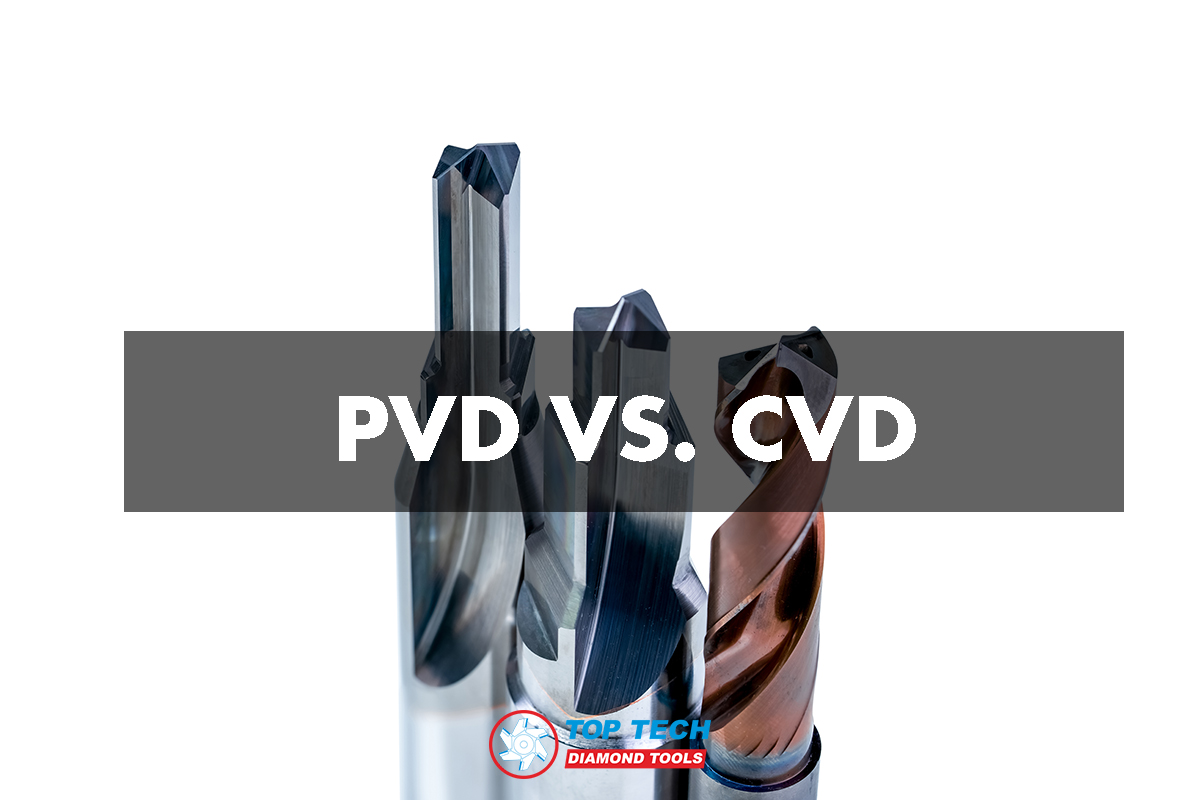
PVD VS. CVD
To use the cutting tool, if you want to increase durability and longer tool life, there is one of the most popular processes is “coating”. There are two main terms, “PVD” and “CVD” coatings. We will explain how these two processes differ, and what are the advantages and disadvantages of those two.
What is ‘coating’? Why do you need a coating for cutting tools?
Coating is a process which will coat an object or a tool with a thin film layer. Usually, this will use the process, called ‘vapor deposition’. The coated layer will help the cutting tool body to be more durable, which results in longer tool life and reduction in production costs.
What is PVD Coating?
PVD coating uses a physical process, which must be done at a high temperature of about 250°-750° C. The coated layer usually has a high hardness, and is also greatly resistant to corresion. It is also resistant to high temperature cutting, and the coated layer is also resistant to evaporation. In addition, PVD coating is a process that “Eco-friendly” compared to CVD coating.
Although PVD coating can greatly improve cutting tool performance, but it still has these following disadvantages;
1. This process is quite costly.
2. This process is a “line of sight”, making it unsuitable for coating the workpiece on the invisible side.
3. The process is quite time consuming.
What is CVD Coating?
CVD stands for ‘Chemical Vapor Deposition’. CVD coating uses a chemical process to create a high-purity coating, which must be done at temperatures up to 1000°C, and must be done in a specialized laboratory to prevent the dangers arising from volatile substances in the process.
The layer quality of the CVD coating is more resistant to abrasion and wear than PVD coating. CVD coating is also suitable for coating irregularly shaped surfaces such as drill bits, end mills or other threading equipment. It can also be used as a coating to create semiconductor for electrical equipment as well.
Although CVD coating can greatly improve cutting tool performance, but it comes with a disadvantage that CVD-coated equipments are more fragile than PVD-coated ones due to residual tensile stress during the process.